Tag: Manufacturing
Walk into any modern factory today, and you will notice something different. No noisy jungle of machines. No conveyor belts. No caution tape. It is alive—with sensors, data dashboards, and smart devices all working in perfect harmony. So what’s really happening? It is digital transformation in manufacturing! And what’s powering it beneath all the blinking lights and high-tech gear? Not just automation. Not just AI.
But something more fundamental and flexible: custom software for manufacturers.
Would you like to know how custom software development impacts the manufacturing industry? This is a great question to ask—and it is one that deserves a deeper dive than just “it improves efficiency.”
This is because in a world where milliseconds matter and errors can cost millions, manufacturers are trading in cookie-cutter tech for customized digital tools that fit like they were built in-house. This blog discusses the why and how.
Why Off-the-Shelf Tools Are Not Built for Today’s Manufacturing
Off-the-shelf software might work fine for smaller businesses or simpler workflows. Does it work when you are trying to juggle multiple vendors, unpredictable supply chains, compliance headaches, and razor-thin margins?
Not really, that is when the cracks start showing.
One Size Doesn’t Fit Anyone
Generic tools are like buying sneakers in “one universal size.” Great in theory—useless in practice.
Your workflows are unique. Whether you are assembling high-precision auto components or crafting handmade soap, your challenges are different. Your systems should reflect you, not the average of everyone else.
Your Old Systems Don’t Want a New Stranger
Many manufacturers still rely on older, legacy systems. These may be clunky, but they work. Introducing a plug-and-play app that can’t “speak” their language? That creates silos and communication breakdowns.
What you need is manufacturing process optimization software that knows how to bridge the old and new, without breaking everything in the process.
You Need to Grow Fast—Not Wait for Updates
Markets shift. Product lines change. New regulations show up uninvited. Standard software just does not pivot fast enough. You are left with a system that ages faster than it improves.
On the other hand, custom solutions grow with you. Want to add a new plant? No problem. You need to integrate with a supplier in another country? Done.
Question worth asking: Why stick with software that asks you to adapt, when you can build one that adapts to you?
Control Should Be Yours—Not the Vendor’s
Let’s be real: when you’re using commercial software, the vendor decides when you get updates, what features are prioritized, and how fast bugs are fixed.
But with custom ERP for manufacturers, you’re in control. You steer the roadmap. You set the priorities.
Power Your Manufacturing With Modern Approaches Turn To Custom Software Development and Deploy The New-age Technologies
Custom Software: The Real Backbone of Modern Manufacturing
How Custom Software Development Impacts the Manufacturing? It becomes your edge. Your secret weapon. Your advantage.
Real-Time Production Visibility
Imagine seeing, in real time, every machine’s status, every order’s progress, and every bottleneck in your system—before it slows you down.
Successful digital work management (DWM) systems deliver value by increasing the efficiency of internal and external maintenance labor, reducing planned downtime through shutdown and outage optimization, and providing the opportunity to upskill the maintenance workforce. Taken together, these levers can lead to cost reductions of 15 to 30 percent.
That’s not a pipe dream. That is what happens when you invest in smart manufacturing solutions tailored to your workflow.
And the best part? You are not reacting anymore. You’re anticipating. Which means faster decisions and fewer errors. Think of it like upgrading from a map to GPS—you’re no longer guessing where the traffic is.
Predictive Maintenance: Don’t Just React—Prevent
Downtime is the silent killer of productivity. One broken machine can throw your perfect plan off track.
Across a wide range of sectors, it is not uncommon to see 30 to 50 percent reductions in machine downtime, 10 to 30 percent increases in throughput, 15 to 30 percent improvements in labor productivity, and 85 percent more accurate forecasting.
With manufacturing process optimization software, predictive maintenance becomes standard. Smart sensors detect patterns, algorithms flag anomalies, and you get alerts before a breakdown happens.
That’s the power of custom software. It doesn’t just report problems. It prevents them.
Data That Means Something
It is really not about how much data you collect. It is about how quickly and clearly you can act on it.
Custom systems help you visualize the right KPIs at the right time—no fluff, no clutter. That means managers, machine operators, and execs all work from the same truth, in real time.
Integrated Supply Chain Management
Manufacturing does not stop at the factory floor. Obtaining goods, logistics, and inventory play a huge part. With custom ERP for manufacturers, every part of your operation—from vendor management to delivery schedules—can be unified in one place.
That means no more double data entry or emailing spreadsheets back and forth.
Remote Monitoring & IoT Integration
With smart sensors, wearables, and IoT devices becoming the norm, manufacturers need systems that can gather, analyze, and respond to data from hundreds of sources. Custom solutions can be designed to connect to all your devices and give you complete remote control.
Whether you’re on the factory floor or across the globe, you’ll stay in the know.
Benefits of Custom Software in Manufacturing
We have seen how custom tools work. Now let’s talk about why they are worth every penny.
1. Higher Operational Efficiency
Automated processes, data accuracy, and real-time updates mean fewer delays, less rework, and smarter use of resources.
2. Cost Savings in the Long Run
Yes, there is an upfront investment. But custom software reduces errors, minimizes downtime, and boosts productivity—saving you more over time than you’d spend fixing issues with generic tools.
3. Competitive Edge
When you are running lean, responding fast, and making data-backed decisions, you naturally outperform the competition. That’s what digital transformation in manufacturing is all about—staying ahead of the curve.
4. Customer Satisfaction
Faster delivery times, better quality control, accurate tracking, and clear communication? That’s what your customers love. Custom software makes it possible.
The Hidden Wins: What Most People Miss About Custom Software
Everyone talks about efficiency and automation. Sure, those are important. But here is the gold that is every so often unnoticed:
1. Retain the Intelligence in Your Organization
Your top engineers and operators know the quirks of every process. But what happens when these stalwarts leave or retire?
With custom ERP for manufacturers, their insights become part of the system. Their problem-solving logic becomes code. Their workflow gets preserved—not lost.
2. Improve Team Morale and Adaptability
Let’s face it: people resist clunky software. But when tools are designed around how they already work, adoption goes up. Frustration goes down. Teams enjoy using the tools they’re provided.
Thought to reflect on: Are your tools helping your people work smarter—or just adding digital friction?
3. Differentiate Yourself from Competitors
Your competition might have access to the same machines, the same suppliers, maybe even the same customers. But what they do not have is your custom-built software system that reflects your way of doing things.
That is your edge. That is what turns good into great.
Case Study Spotlight: A Real-World Win
Let’s look at a real example.
One of Fingent’s clients—Lakeside Cabins—wanted to streamline their processes and deliver faster with more accuracy. They also wanted to modernize their approaches and offer unique experiences for their customers.
Fingent helped the client deploy 3D Configurators that enabled them to involve their customers through their web portal in designing the cabins at each stage of production. The customers felt more included and valued, plus the manufacturing outcomes were more error-free and sustainable.
That’s smart manufacturing solutions in action.
3D Web Configurator For Cabin Design
How Should Manufacturers Handle Custom Software?
If you are considering taking the leap, here are some initial steps you can begin with:
Audit your current systems.
What’s working? What’s not? Talk to your team. Gather feedback.
Identify your biggest pain points.
Focus on the challenges that are costing you time or your precious resources.
Start small but think big.
You don’t need a full-blown overhaul overnight. Begin with one system or process and scale up.
Choose the right partner.
Custom software is only as good as the team building it. Partner with a firm that has manufacturing experience and a consultative approach.
Why Fingent?
At Fingent, we don’t just write code. We solve problems.
Having years of experience in digital transformation in manufacturing, we comprehend the distinct challenges of the industry. Our team collaborates closely with clients to create customized tools that produce significant effects—from the factory floor to the executive suite.
We combine the strength of manufacturing process optimization tools, tailored ERP for producers, and adaptable, intelligent manufacturing solutions to develop systems that not only function—they perform miracles. From streamlining operations to modernizing legacy infrastructure, we ensure every solution is future-ready, not just functional.
And we do not believe in copy-paste tech. We trust in tailor-made excellence—software that feels as if it was designed specifically for you.
Whether you’re delving into automation, dealing with obsolete processes, or set to streamline your entire production pipeline, our team is prepared to dive in and start building.
Final Take: Don’t Buy the Future—Build It
Digital transformation in manufacturing is not just about modernizing. It’s about redefining how you compete.
Custom software is no longer a luxury. It’s the blueprint for the next generation of manufacturers. It’s about rethinking everything—from supply chain to shop floor—in a way that fits your DNA.
So here’s the question:
Are you still trying to retrofit your factory to someone else’s software—or are you ready to build tools that are made for you, by you, and grow with you?
Want to transform your operations with tailor-made tools? Then don’t follow the crowd—lead it. Let Fingent be your partner in progress. Let’s build something powerful together.
Stay up to date on what's new
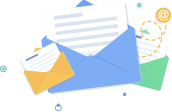
Featured Blogs
Stay up to date on
what's new
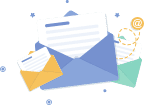
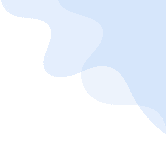
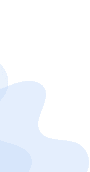
Talk To Our Experts
Manufacturing has long been a driver of global prosperity and economic growth. We all see astounding growth as the manufacturing industry evolves and keeps up with changing consumer needs.
This has led industry leaders to shift their focus from traditional to smart factory technology. A smart factory offers many benefits to operators, managers, and executives of companies in this industry. And yet, a few companies hesitate to start their journey the ‘smart way.’ If you are one of those companies, this article will help you with details and show you how a smart factory can bring its business operations and customer satisfaction to a new level.
Let us begin by understanding what a smart factory is.
What Is a Smart Factory?
Take a manufacturing facility and completely digitize it – that is what a smart factory is. The smart factory is a digitized manufacturing facility that uses digitized manufacturing methods, devices, and systems to continuously collect and share data. This data is used to make informed decisions that improve processes and address manufacturing challenges. The smart factory is a new industrial revolution phase focusing on real-time data, connectivity, automation, and Machine Language.
A smart factory uses the best digital and physical worlds to monitor the entire production line, from supply chain management to manufacturing tools. It can even monitor the work of an individual operator on the factory floor.
Why Is It Smart to Embrace the Smart Factory Movement?
According to a press release by Marketsandmarket, the smart manufacturing market was projected to reach USD 228.2 billion by 2027. It is expected to grow at a CAGR of 18.5% from 2022 to 2027. Then, most businesses consider smart factories highly beneficial and crucial across industries and sectors. Here are some of those significant benefits:
- Measure key performance indicators: A smart factory provides managers with automated data that is accurate. This data gives them the ability to measure key performance indicators more efficiently.
- Think ahead better and faster: Smarter predictive maintenance allows managers to predict and resolve maintenance issues better and faster.
- Efficient demand management: It can forecast more accurately and thus reduce waste enabling efficient demand management.
- Boosted productivity: Managers boost productivity as it can provide seamless data on machine maintenance and potential bottlenecks.
Key Elements of a Smart Factory
There are a few elements that make the smart factory what it is. Understanding these elements will help you see how it fits into your business.
1. Robotics
Robotics is a crucial element of a smart factory. Robotics enables smart material handling and adaptive operations. Besides, robots come with flexible infrastructure that can scale depending on business needs.
2. Big data and IoT
The Smart factory provides augmented access to large amounts of data obtained through the cloud and connected devices. This can empower manufacturers to identify patterns and insights, thus enabling them to make more informed decisions to optimize operations and improve productivity in the long run.
3. Cloud-based management
Cloud-based management includes a suite of professional software architecture that can be developed to empower highly efficient business operations. This can offer market reactivity and scalability. It can also provide real-time visibility into a business’s inventory and manage supply chain operations from the manufacturing to the end customer.
4. Virtual reality
Manufacturers have been using virtual reality for some time now. It uses computer-generated visuals that help improve the experience of the user. It trains engineers to handle complex virtual processes, maintenance systems, and troubleshooting.
5. Cybersecurity
Smart factories tend to increase cyber security threats. Thankfully, smart factory technologies are equipped to streamline cyber threats. For example, AI-powered bots act as guards 24/7, ensuring data security.
6. Additive manufacturing
Additive manufacturing is used for rapid prototyping, on-site manufacturing, and more. It saves time and costs spent on production and tool replacements. Quick reproduction, reconfiguration, and validation can also enable reverse engineering.
Read more: ERP Systems for Manufacturing: How it Improves Business Process
A Look into The Future of Smart Factories
Manufacturers that leverage smart factory technologies will unlock game-changing flexibility and agility. Emerging imperatives for the manufacturing industry include supply chain resilience, enhanced productivity, flexibility, and sustainability. In simple terms, only those manufacturing systems that enable a demand-driven and dynamically optimized value chain will survive and thrive.
1. Increasing demands
In the coming years, factories will face more stringent regulatory and compliance requirements ever. Such demands also merge with global trends toward adopting digitization. Given their ability to drive exponential productivity and sustainability benefits, digital technologies are at the heart of these changes.
2. Automation and beyond
Across the world, manufacturers began their digital transformation with automation to minimize manual operations and maximize output. But technological advances are enabling manufacturers to empower operators to understand operational data. Furthermore, newer platforms and integration technologies are driving down the cost of digital transformation.
3. Transformational gains
By implementing an integrated automation system, manufacturers can accelerate their sustainable manufacturing vision. Driven by the unrelenting need for agility and resilience, manufacturers can empower their workforce by adopting smart factories. By building future smart factories, they can unlock value benefits for all stakeholders along the way.
Creating a Smarter Future for Manufacturing with Fingent!
A smart factory is a direct way for manufacturers to excel in a competitive and dynamic marketplace. Partnering with the right app development company could mean make or break for you. Manufacturers need the right partner to help them implement solutions correctly. Fingent has been a consulting partner to several manufacturing companies and proved its mettle. Have a look at our Case Studies:
With the right partner, upgrading a traditional factory to a smart factory is much simpler than most imagine. Fingent builds custom solutions to integrate factories with smart solutions. Through our experience, we have already helped many businesses transform their traditional factories into smart factories.
Our experts at Fingent can help retrofit most existing manufacturing equipment and set up a centralized hub that can receive data from all the sensors. A cloud service could be set up to monitor and analyze from offsite. What is more, these solutions are upgradeable.
This allows established factories to upgrade at their own pace while keeping the upgrade cost low. Do you have a traditional factory that needs to become smart? Contact Fingent today!
Stay up to date on what's new
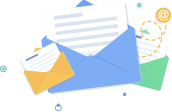
Featured Blogs
Stay up to date on
what's new
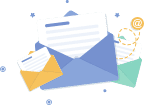
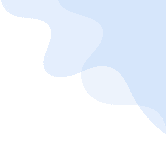
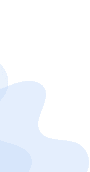
Talk To Our Experts
The COVID-19 pandemic has accentuated the need for resilient supply chains and human-machine collaboration at work. Full or partial shutdowns, as well as social distancing regulations, impose factories and workspaces to operate with the minimal onsite crew. Despite labor shortages, supply chain disruptions, and other production challenges, manufacturers are under constant pressure to respond to the evolving market needs. The demands for mass customization, quality expectations, faster product cycles, and product variability are at an all-time high. Tackling these persistent challenges requires combining human skill and ingenuity with the strength and speed of robots. To bring the best of both worlds – human creativity and robotic precision – manufacturers should adopt cobots (collaborative robots) that can reduce human interaction in feasible situations and accelerate production cycles.
Cobots allow manufacturers to maximize production and address the changing demands while ensuring the safety of their employees, clients, and partners. Why are cobots the future of manufacturing? How do they help build manufacturing resilience? Let’s explore further in this blog.
Read more: What are cobots and how can they benefit industries
Cobots Enhance Manufacturing Efficiency
Collaborative robots or cobots are designed to safely work alongside humans in tedious, dull, and hazardous environments. Unlike the traditional industrial robots that work in fenced premises to avoid close proximity with people, cobots operate in a shared workspace alongside human labor. For instance, a robot that helps humans sort foam chips in a lab is a cobot, while a robot welding a sharp cutting tool in a restricted factory area is a typical industrial robot.
Conventional industrial robots have long enabled manufacturers to leverage automation and compensate for labor shortages, but they are typically designed to execute one specific task. Moreover, they lack the cognitive capabilities possessed by humans to reprogram their operations based on new circumstances. In contrast, cobots don’t require heavy, pre-programmed actuators to drive them. Cobot motions are steered by computer-controlled manipulators, such as robotic arms, which are supervised by humans. Thus, cobots facilitate effective human-machine collaboration at work.
Cobots can be programmed to perform a wide range of tasks in a factory setting such as handling materials, assembling items, palletizing, packaging, and labeling, inspecting product quality, welding, press-fitting, driving screws and nuts, and tending machines. While cobots attend these mind-numbing jobs, human workers can focus on tasks that require immense resourcefulness and reasoning.
Read more: Digital Transformation in Manufacturing
Benefits of Cobots in Manufacturing
Modern manufacturing requires effective human-machine collaboration to cut expenses, reduce time-to-market, and address growing customer demands. Here’s how cobots empower manufacturing enterprises.
1. Easy to Deploy and Program
It takes days and weeks to install and program a traditional industrial robot. A cobot, on the other hand, can be set up in less than an hour. They are lighter than conventional robots. With user-friendly mobile applications and customized software, you can swiftly program the cobot to get started. Right software configurations enable cobots to learn new actions, without any specialized training. Using intuitive 3D visualizations or simple graphical representations, you can move the robot arm to preferred waypoints. Your employees can focus on more critical tasks while the cobot takes care of mundane jobs.
2. Flexible to Perform Different Tasks
Cobots can be easily shifted from one workstation to another due to their flexible hardware. With minimal software customizations, cobots can be re-deployed or repurposed to perform different functions across various departments. For example, a cobot that performs picking and packing can be re-programmed as a filler by replacing its robotic arm with a tube and nozzle.
Read more: Challenges, Opportunities, and Technologies That Will Revolutionize Manufacturing
3. Save Production Cost and Time
A study conducted by the World Economic Forum in association with Advanced Robotics for Manufacturing found that collaborative robots can cut nearly two-thirds of the cycle time required to pack boxes onto pallets. Because cobots are designed to work without any breaks, they reduce the idle time between cycles. The International Society of Automation reports that cobots can save production costs by reducing 75% of manual labor. Traditional robots increase the installation costs for manufacturers as they need to set up additional safety measures around the deployment area. Cobots don’t incur such extra expenses as they can be set up in close proximity to humans.
4. Improve Employee Engagement and Productivity
Cobots work in collaboration with people to refine and process the tasks better. They can never replace the human touch in production. When cobots take care of repetitive tasks such as screwing a bottle or packing medical equipment, employees can focus on more important functions such as running quality checks or inspecting a worksite. It allows manufacturers to optimize their productivity and boost employee morale. Businesses can also prepare their workforces to learn new skills.
5. Maintain Consistency and Accuracy
From the first to the hundredth task, cobots maintain the same level of accuracy and consistency. Humans can get drained easily, whereas a cobot never deviates from the actions for which it is set up. This helps ensure high product quality and uniformity. With the right software and hardware configurations, cobots can produce more finished goods at an incredible pace, faster than handcrafting.
Cobots and The Future of Manufacturing
Industry 4.0 paved the way for automation and smart manufacturing powered by data-driven technologies such as IoT, cyber-physical systems, wearables, AR, cloud computing, artificial intelligence, cognitive computing, and so on. Though the sole focus of Industry 4.0 is to improve process efficiency through physical and digital integration, it accidentally ignores the significance of human value in process optimization. Industry 5.0 re-shifts its focus on human value by fusing the roles of mechanical components and human workers in production. This makes cobots the very foundation of the next wave of the industrial revolution, that is, Industry 5.0.
Denmark-based Universal Robots reports that cobots are at the heart of Industry 5.0. Cobots democratize robotic capabilities, thereby serving as a personal tool that can be leveraged by any member of the workforce to apply creative skills and generate more value. Cobots can be used as a plug-and-play solution across a variety of manufacturing and industrial operations such as automotive production, food processing, chemical plants, medical devices, and kits, among others.
Since they collaborate well with humans in a safe environment, cobots will:
- augment intelligent decision-making,
- drive high-quality products to the market,
- enable mass customization and personalization,
- optimize manufacturing costs,
- generate new job roles (eg: Chief Robotics Officer), and
- boost virtual education to make the most of collaborative robotics.
Read more: How Custom Software Development Helps Manufacturing Industry
How We Help Manufacturers Leverage Cobots and Other Emerging Technologies
As technology matures, manufacturing enterprises need to build use cases that prove the inevitability of human-robot collaboration. We help develop POCs and use cases that demonstrate how your business can benefit from cobots. Our experts can develop your cobot management software or mobile app from scratch or customize your existing software to address the evolving market demands. Fingent can work along with your cobot hardware manufacturers to develop a robust software orchestration layer that can control the movement of your cobots. We also simplify the training process to help you get started in no time.
Stay up to date on what's new
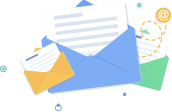
Featured Blogs
Stay up to date on
what's new
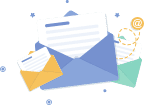
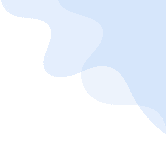
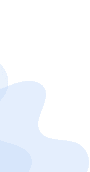
Talk To Our Experts
As the world deals with the short and long-term effects of Coronavirus, the manufacturing industry has suffered significant challenges during 2021. This knock-on effect is likely to be felt into 2022 as consumer demand and spending habits have transformed during the pandemic.
The pandemic demonstrated that major events can have a profound impact on manufacturing operations. Fluctuations between local and national lockdowns have directly impacted the manufacturing industry. Among various other things, it has led to delaying tax bills, postponed mortgage payments.
Knowing what challenges await manufacturing industries will help you and your team come up with the best strategy to achieve success in 2022. So, this article will cover some of the biggest challenges manufacturing industries will face in 2022. We will also look into how these industries can approach the challenges with the help of technologies.
Top challenges prevailing in the manufacturing industry-2022
1. Need to increase sales and revenue
The pandemic made businesses lose several thousands of dollars pushing manufacturing industries to put extra effort into recouping financial losses. Some companies chose to double up on their marketing efforts.
However, the right step would be to create a strategy to start building the business’s pricing power. Building a price power is the surest way to enjoy sustainable earnings.
2. Labor retention
The pandemic era has made it challenging to tackle labor retention issues among the workforce. As the pandemic continues, it is become increasingly hard to find experienced and motivated workers.
To complicate matters, with a fair portion of workers are nearing retirement manufacturing industries are facing a looming shortage of skilled labor. The newer technologies require a workforce with top-tech skills.
3. Customer self-service capabilities
Manufacturers are ever concerned about delivering their products to customers on time. Though the technology makes it possible for customer self-service capabilities, it is not commonly used.
Customers find it frustrating to constantly contact manufacturers for updates on their orders, requests for new proposals, and so on. Customers prefer immediate access to information.
You can address this issue by simply keeping the needed data for customers in a self-service portal. This will allow your customers to retrieve a solution. Plus it can enable the sub-contractor to track and accept tasks assigned to him without bothering anyone.
4. Maximizing work with minimum staff
The social distancing protocol due to the pandemic has forced manufacturing companies to run the factories with lesser staff. This is the time to explore the implementation of more automation technologies.
Read more: Top 10 Technologies That Will Transform Manufacturing!
Most-followed technologies that enable manufacturers to stay on top of the challenges
As Industry 4.0 is still in progress, most manufacturing industries are shifting gears in an effort to automate their manual processes. And the challenges are accelerating this shift now more than ever. Take a look at the top opportunities new technologies bring to the manufacturing industry.
1. Machine Learning and Artificial Intelligence capabilities
The biggest asset of any company is its data. It is vital to use algorithms to use this enormous amount of data effectively. Humans cannot do this task as efficiently, quickly, and accurately as by AI-led technologies. This ensures your manufacturing is more productive and less wasteful.
According to a global survey conducted by McKinsey & Company, 44% of respondents report cost saving from AI adoption.
2. 3D printing
Manufacturing companies can greatly benefit from 3D printing technology as it can enable manufacturers to make faster and cheaper prototypes.
It can double the performance while lowering the cost by half. It is a cost-effective way to troubleshoot or test the products. It also enables manufacturers to produce products that are in high demand.
3. Smart factories with 5G
The fourth industrial revolution is ushering in an era of smart manufacturing that is enabled with connected devices over 5G networking.
These can make decentralized decisions as the 5G mobile network is faster and more powerful. It is capable of handling full integration of all the devices in a smart factory making it a default choice of manufacturers.
4. Internet of Things
Industrial IoT makes it possible to interconnect sensors and electronic devices that collect and exchange data. It drives AI and performs predictive analytics. IoT is changing the way products are made and delivered.
A study conducted by MPI Group revealed that roughly 63% of manufacturers believe that applying the IoT to products will increase profitability over the next five years.
5. Predictive maintenance
The manufacturing industry depends heavily on predictive maintenance technology. In the past, routine maintenance checks were scheduled to detect unnoticed malfunctions. But that would halt the production and cost money.
Today’s digital technology has enabled machines to send messages to notify workers if or when maintenance is required. These real-time alerts equip the maintenance team to identify and correct mechanical failures without downtime.
6. Shift in the scope of the job
As technology takes over repetitive tasks, employees will need new skills. These skills would include data analysis, software engineering, programming, customer service. R&D and product development, and so on.
7. Agility and responsiveness
Changing customer demands and market conditions require manufacturers to focus on improving responsiveness and agility. Responsiveness and agility are achieved when the time to create, receive, schedule, and process a customers’ order is reduced.
This will enable manufactures to match production cycles and product demand levels. Matching these two aspects can help manufactures pump their operations with greater agility.
Read more: ERP Systems for Manufacturing: How it Improves Business Process!
Fingent can help revolutionize your manufacturing company
Identifying improvement opportunities can help your manufacturing industry enjoy significant benefits. Fingent can help you improve your business process and facilitate growth toward building an incredibly smart manufacturing plant.
Fingent is an efficient web and mobile app development company with vast experience in crafting remarkable digital success stories for diverse manufacturing companies across continents.
We will help you to stay abreast with what may affect your business and provide you with potential solutions available. To help plan for 2022 contact Fingent!
Stay up to date on what's new
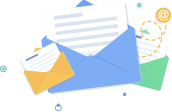
Featured Blogs
Stay up to date on
what's new
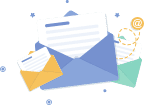
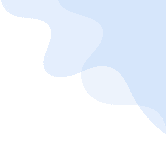
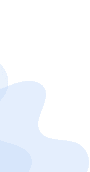
Talk To Our Experts
Manufacturing technologies set to hold the reins in 2021
From big data analytics to advanced robotics to computer vision in warehouses, manufacturing technologies bring unprecedented transformation. Many manufacturers are already leveraging sophisticated technologies for manufacturing such as the internet of things(IoT), 3D printing, Artificial Intelligence, etc., to improve operations’ speed, reduce human intervention, and minimize errors.
As 2021 rapidly approaches, manufacturers will have to move away from Industry 4.0 and embrace Industry 5.0. The latter is all about connecting humans and machines (smart systems). Interestingly, Industry 5.0 may already be here. The ongoing COVID-19 pandemic only accelerates its arrival.
Read more: Digital Transformation in Manufacturing
Here are the top 10 technologies that positively impact the manufacturing industry.
1. Robotics
With advances in robotics technology, robots are more likely to become cheaper, smarter, and more efficient. Robots can be used for numerous manufacturing roles and can help automate repetitive tasks, enhance accuracy, reduce errors, and help manufacturers focus on more productive areas.
Benefits of Using Robotics in Manufacturing:
- They improve efficiency right from handling raw material to finished product packing
- You can program robots to work 24/7, which is excellent for continuous production
- Robots and their equipment are highly flexible and can be customized to perform complex jobs
- They are highly cost-effective even for small manufacturing units
Collaborative assembly, painting, and sealing, inspection, welding, drilling, and fastening are a few examples of the jobs done by robots. Today, robots work in several industries, including rubber and plastic processing, semiconductor manufacturing, and research. While they are mainly used in high-volume production, robots make their presence felt in small to medium-sized organizations.
Read more: What Are Cobots and How Can They Benefit Industries?
2. Nanotechnology
Nanotechnology has grown to a great extent in the last few years. It involves the manipulation of nanoscopic materials and technology. Though its widespread use is relatively new, it will be indispensable to every manufacturing industry soon. Further research and experimental designs suggest that nanotechnology can be highly effective in the manufacturing industry.
Applications of Nanotechnology in Manufacturing:
- Create stable and effective lubricants that are useful in many industrial applications
- Car manufacturing
- Tire manufacturers are using polymer nanocomposites in high-end tires to improve their durability and make them wear resistance
- Nanomachines, though not used widely in manufacturing now, are, for the most part, future-tech
3. 3D Printing
Post its tremendous success in the product design field, 3D printing is set to take the manufacturing world by storm. The 3D printing industry was worth USD 13.7 billion in 2019 and is projected to reach USD 63.46 billion by 2025. Also known as additive manufacturing, 3D Printing is a production technology that is innovative, faster, and agile.
Benefits of Using 3D Printing in Manufacturing:
- Reduces design to production times significantly
- Offers greater flexibility in production
- Reduces manufacturing lead times drastically
- Simplifies production of individual and small-lot products from machine parts to prototypes
- Minimizes waste
- Highly cost-effective
Major car manufacturers use 3D printing to produce gear sticks and safety gloves.
Read more: 3D Printing: Fueling the Next Industrial Revolution
4. The Internet of Things (IoT)
IoT in manufacturing employs a network of sensors to collect essential production data and turn it into valuable insights that throw light into manufacturing operational efficiency using cloud software. This connectivity had brought machines and humans closer together than ever before and led to better communication, faster response times, and greater efficiency.
Benefits of Using IoT in Manufacturing
- Internet of Things (IoT) reduces operational costs and creates new sources of revenue
- Faster and more efficient manufacturing and supply chain operations ensure a shorter time-to-market. For instance, Harley- Davidson leveraged IoT in its manufacturing facility and managed to reduce the time taken to produce a motorbike from 21 hours to six hours.
- IoT facilitates mass customization by providing real-time data essential for forecasting, shop floor scheduling, and routing.
- When paired with wearable devices, IoT allows monitoring workers’ health and risky activities and making workplaces safer.
The ongoing pandemic has expanded the focus on IoT due to its predictive maintenance and remote monitoring capabilities. Social distancing makes it difficult for field service technicians to show up on short notices. IoT-enabled devices allow manufacturers to monitor equipment’s performance from a distance and identify any potential risks even before a malfunction occurs. Additionally, IoT has enabled technicians to understand a problem at hand and come up with solutions even before arriving at the job site so that they can get in and get out faster.
Read more: Upcoming IoT trends that can shape the business landscape
5. Cloud Computing
After making its presence felt in other industries, cloud computing is now causing ripples in manufacturing. From how a plant operates, integrating to supply chains, designing and making products to how your customers use the products, cloud computing is transforming virtually every facet of manufacturing. It is helping manufacturers reduce costs, innovate, and increase competitiveness.
IoT helps improve connectivity within a single plant, while cloud computing improves connectivity across various plants. It allows organizations across the globe to share data within seconds and reduce both costs and production times. The shared data also helps improve the product quality and reliability between plants.
Read more: Why It’s Time to Embrace Cloud and Mobility Trends To Recession-Proof Your Business?
6. Big Data
The manufacturing industry is complicated in terms of the variety and depth of the product. As far as opening new factories in new locations and transferring production to other countries is concerned, companies can leverage big data to tackle it.
As the process of capturing and storing data is changing, new standards in sharing, updating, transferring, searching, querying, visualizing, and information privacy are arising. Think of manufacturing software like MES, ERP, CMMS, manufacturing analytics, etc. When integrated with big data, these can help find patterns and solve any problems.
Benefits of Using Big Data:
- Improve manufacturing
- Ensure better quality assurance
- Customize product design
- Manage supply chain
- Identify any potential risk
Explore our use case: Adding New Dimensions to Equipment Maintenance with IIoT, AR, and Big Data
7. Augmented Reality
In manufacturing, we can use AR to identify unsafe working conditions, measure various changes, and even envision a finished product. Augmented Reality can help a worker view a piece of equipment and see its running temperature, revealing that it is hot and unsafe to touch with bare hands. An employee can know what’s happening around them, like what machinery is breaking down, a co-worker’s location, or even a factory’s restricted sites. Simply put, AR applications can help inexperienced employees to be informed, trained, and protected at all times without wasting significant resources.
AR has made it possible for technicians to provide remote assistance by sending customers AR and VR enabled devices and helping them with basic troubleshooting and repairs during the COVID-19 crisis. Also, more and more customers are open to allowing manufacturers to implement AR with the long-term goal of creating permanent solutions. After all, it helps both the customers and field technicians by reducing the risk of exposure.
Read more: How Augmented Reality Can Simplify Equipment Maintenance
8. 5G
5G will have a tremendous impact on the manufacturing industry. It will be more transformational for devices that drive automated industrial processes.
The amazing low-latency and connectivity of 5G will power sensors on industrial machines. It will help generate a lot of data that will open new avenues of cost savings and efficiency when combined with machine learning. Currently, China and South Korea are leveraging 5G this way. Soon the US and the UK are expected to compete with them.
Read more: From Remote Work to Virtual Work, 5G is Reinventing the Way We Work
9. Artificial Intelligence(AI)
Manufacturers are already employing automation on the plant floor and in the front office. In the future, AI-powered demand planning and forecasting will continue to develop that will help manufacturers align their supply chain with demand projections to get data that were not possible previously.
A study from IFS shows that 40% of manufacturers plan to implement AI for inventory planning and logistics and 36% for production scheduling and customer relationship management. 60% of the respondents are said to focus on productivity improvements with these investments.
Read more: The Future of Artificial Intelligence – A Game Changer for Industries
10. Cybersecurity
Moving manufacturing operations to the cloud and building and integrating systems using IoT will equally create opportunities and challenges. In an increasingly insecure digital era, there is a pressing need for heightened security.
Manufacturing experts are investing in secure cloud-based ERP like SAP and Odoo to resolve the security challenges. Enterprises-big or small- will soon increase their dependence on cloud-based ERP systems to address security glitches and save costs by paying for usage.
Read more: Top 6 Reasons Why You Should Move to a Cloud-Hosted ERP
White Paper: What difference does RPA bring to your business? How can you embrace this disruptive technology to remain competitive? Download to learn more!
Conclusion
Technologies for manufacturing will decrease labor costs, improve efficiency, and reduce waste, making future factories cheaper and more environment-friendly. Additionally, improved quality control will ensure superior products that will benefit both the consumers and the manufacturers.
COVID-19 has changed the way the manufacturing industry operates. If your business wants to remain competitive, you will have to embrace manufacturing technologies to shape your company’s future. To know more about the forward-thinking strategies that integrate the latest trends and technologies, please connect with us today.
Stay up to date on what's new
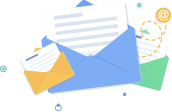
Featured Blogs
Stay up to date on
what's new
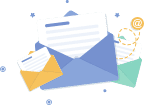
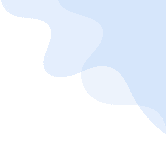
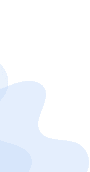